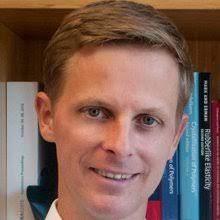
Professor Christian Linder is the principal investigator of the Computational Mechanics of Materials Lab at Stanford University. He received his Ph.D. in Civil and Environmental Engineering from UC Berkeley, an M.A. in Mathematics from UC Berkeley, an M.Sc. in Computational Mechanics from the University of Stuttgart, and a Dipl.-Ing. degree in Civil Engineering from TU Graz. Before joining Stanford in 2013, he was a Junior
Professor of Micromechanics of Materials at the Applied Mechanics Institute of Stuttgart University, where he also obtained his Habilitation in Mechanics. Notable honors include a Fulbright scholarship, the 2013 Richard von-Mises Prize, the 2016 ICCM International Computational Method Young Investigator Award, the 2016 NSF CAREER Award, and the 2019 Presidential Early Career Award for Scientists and Engineers (PECASE).
The study of fracture in materials is inevitable in fields like engineering and medicine for optimizing the performance and ensuring the safety of structural and biological systems. Interestingly, their unique underlying micromechanisms characterize the failure in different materials. Brittle fracture is observed in certain materials like glass, ceramics, concrete, and even highly stretchable elastomers, wherein catastrophic failure occurs when the material fracture strength is reached. On the other hand, materials like low-carbon steel, aluminum, cast iron, and titanium exhibit ductile failure wherein significant necking behavior are observed before fracture due to plastic yielding. Owing to their broad spectrum of applications and the complexity involved in modeling their behavior, we mainly study the fracture characteristics of steel and rubber-like materials. While the ductile fracture in steel involves the nucleation, growth and coalescence of micro-voids, the fracture in elastomers involves the rupture of the underlying polymer chains. Accurate prediction of their fracture properties necessitates the proper incorporation of the effects of these micromechanisms into the constitutive material formulations. As a result, we present micromechanically motivated continuum approaches for modeling the fracture behavior in steel and rubber-like materials. Due to a large amount of deformation observed in these materials, a finite deformation framework is employed for formulating their constitutive behavior. The commonly used phase field method is coupled for modeling the failure propagation. For the ductile fracture in steel, the contributions from the elastic and plastic strain energies and the crack surface energy are considered for formulating the free energy functional. To account for the effects of stress states and plastic deformation on the fracture properties, the continuum framework is coupled with the stress-weighted ductile fracture model for proposing an evolution of the fracture toughness during crack initiation and propagation. For rubber-like materials, a multiscale continuum model is employed, with the deformations at the two scales bridged using the non-affine microsphere model. At the microscale, polymer chains are modeled to comprise several elastic segments, with the extensibility resulting from the underlying bond distortions. The contributions from the entropic free energy and internal energy due to bond stretch in the microscale chains are considered. In addition to the homogenized chain response, the nonlocal damage effects are considered at the macroscale. The damage evolution is mainly due to the breaking of the constituent monomer molecular bonds. The numerically implemented formulations using the finite element method are validated by comparison of simulation results with experimental data.